Geared up
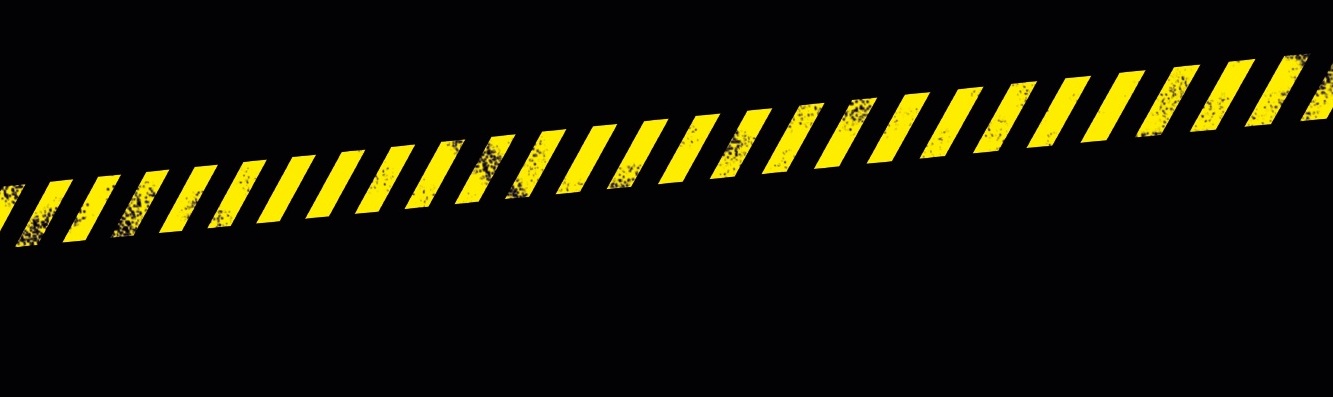
Danny Clarke, head of occupational health and safety at Sound Advice, part of ELAS Business Support, discusses the current health and safety issues affecting the motor vehicle repair industry and offers his advice on how employers can safeguard their working practices.
Over the last five years motor vehicle repair and mechanical service companies have reported over 7,000 injuries and 33 deaths in the industry. The need for employers to manage health and safety risks is high in this sector and businesses need to ensure they are doing everything practically possible to protect health and safety onsite.
Employers operating within this industry can find it challenging to interpret and comply with the various acts and regulations relating to health and safety, and without the expert knowledge to understand their responsibilities, some could find themselves either not complying or introducing overly complicated measures at the expense of business operations.
We are regularly asked to help companies manage occupational health and safety in this industry and, as a result, have developed processes and assessments that not only help companies comply with the law, but also ensure businesses can see the benefits from health and safety.
Common
The most common occupational hazards that we help manage relate to noise, vibration and working with hazardous substances. These areas, in particular, are subject to specific legislation and require the full cycle of risk management, from undertaking initial assessments of exposure and recommending appropriate interventions through to delivering health surveillance that helps ensure control measures are working. This is a truly holistic approach that ensures all parties understand the full degree of risk which, when you consider that between 2012 and 2013 there was a 68% increase in noise induced hearing loss claims, shows that taking steps such as assessments and health surveillance not only helps compliance, but protects the business reputation and finances.
Whilst some employers may see such legal requirements as added pressure on resources, especially in an industry dominated by small-to-medium-sized businesses, the reality is that as an industry it is not just about doing the minimum requirements set by law. An increasing number of employers are taking a more proactive approach to stay ahead of the curve and are seeing the benefits of effective management for their businesses.
Increase
There has also been an increase in the numbers of employers that are undertaking additional assessments, such as musculoskeletal assessments which help to ensure healthy workplaces and pro-actively reduce absence, and biological monitoring for those that work in environments with diesel fumes present.
Employers also need to keep up-to-date with all new legislative and legal requirements, such as the introduction of the Globally Harmonised System change, which will see an update in hazardous substances labelling and is due to come into force in June 2015. Employers need to ensure that they are not only aware of such changes, but provide the necessary training to employees.
As employers take more action, knowing that good working practices show good ethics and in-turn are good for business, there will be a greater demand for additional testing which goes beyond the legal requirements for the industry. This ensures a best standard practice is adopted across all aspects of health and safety.
Although research shows that health and safety in this industry is being taken seriously, with many companies going beyond best practice, there is that overhanging risk of a claim that can have huge financial costs to a business. With this in mind, now more than ever, it is crucial to the motor repair and mechanical services industry to overcome health and safety challenges effectively to protect themselves and their employees with minimal disruption to productivity.