New Airex Process from Roberlo embraces ‘the power of air’
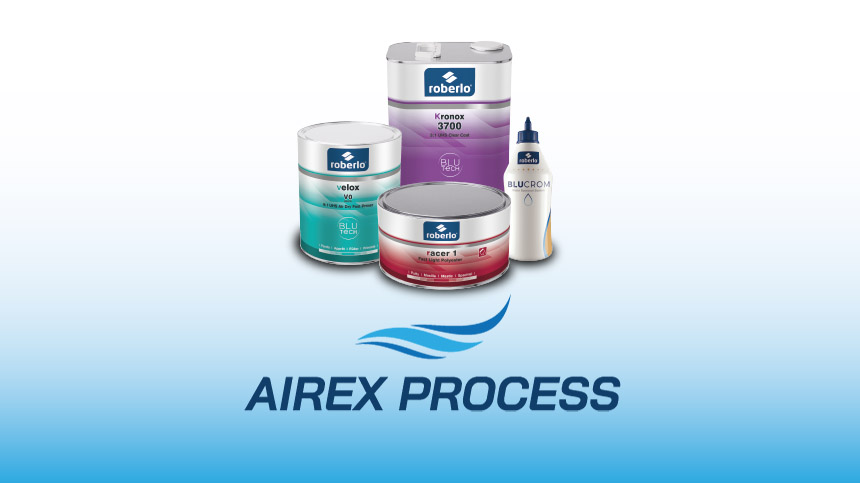
Roberlo has launched the Airex Process, its new repair system which uses “the power of air” to offer an efficient and sustainable solution that reduces energy consumption and optimises drying times.
The Airex Process relies on air as the main tool for drying the solutions that make up the process. Compared to conventional processes, Airex Process reduces repair time by more than 75% compared to conventional air drying systems, according to a Roberlo statement.
Airex Process
This process allows the elimination of booth use, maintaining high levels of efficiency with significant energy savings. The Airex Process also offers high versatility, giving the option to perform booth drying in as little as 10 minutes at a temperature of 40ºC. This means a reduction in booth occupation time of more than 75% and energy savings of more than 65% compared to conventional coatings.
At the heart of this system is the new Kronox 3700 air-drying clearcoat, which stands out for its fast drying times. It is ready to handle at room temperature of 20°C in just 50 minutes, compared to five hours for conventional clearcoats. If forced drying at 40ºC is chosen, the time is reduced to only 10 minutes.
Another important aspect of Kronox 3700 is that it does not require flash-off times between coats. In addition, Kronox 3700 is a product that adapts perfectly to all types of users, being very easy to use and without the need for a hardener. At the same time, its drying is not dependent on humidity, making the product less sensitive and easy to adapt to different types and conditions of repair.
Complementary solutions
Airex Process also includes a range of additional products including:
- Racer 1: An ultra-fast drying, lightweight putty that ensures a high-quality finish in less time.
- Velox: High-speed 2K UHS 6:1 acrylic primer, which enables uninterrupted application, drying and sanding processes.
- Blucrom: Roberlo’s water-based colour system, which stands out for its versatility and cost-saving capacity. In its “efficient” mode, bodyshops can reduce up to 30% in materials and 20% in time.
The combination of efficiency, speed and sustainability makes this system an ideal solution for workshops looking to optimise their processes without compromising the quality of the finish.