Bloodhound gets the 3M touch
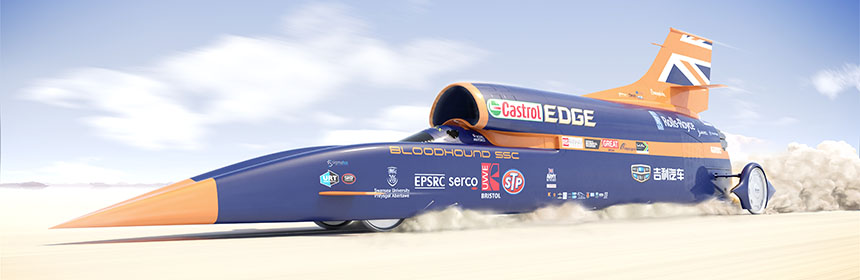
Bloodhound SSC, the supersonic car expected to smash the land speed record, has returned to 3M’s state-of-the-art Atherstone facility for a final paint-job, which will be more than just cosmetic.
Powered by hybrid rockets and a Eurofighter Typhoon jet engine, the Bloodhound SSC will attempt to surpass 1,000mph – faster than a bullet – in South Africa in 2018.
The design team is confident of going well beyond the current land speed record of 763.065mph, set in 1997 by the world’s first supersonic car, the Thrust SSC.
To that end, every aspect of the car has been designed for speed, including the distinctive blue and orange paintwork, which needs to be ultra-smooth and lightweight.
The science-based technology company’s Atherstone facility was chosen as the perfect place for carrying out the work, as it houses a first-class spraybooth and top-of-the-range equipment.
Work on the upper chassis began at the site on 19 December, after the vehicle’s front half was painted there in May 2015. At nearly 5.5 metres long, the titanium-skinned back section is the car’s largest single part. It houses everything behind the cockpit, including the jet engine, rocket motor and air brakes.
Simon Evans, of paintbysimon.com, will spend a week single-handedly spraying the section with a single layer of aircraft paint. Simon has worked on such high-profile projects as the CNN Hummer ‘Warrior One’ and other vehicles for films, as well as appearing on television programmes about cars.
Simon said, ‘The idea is to have the vehicle as smooth as possible to reduce turbulence on the skin, but without adding too much weight to the car. You need first-class facilities, because you can’t have any contamination. Otherwise it would end up looking like the surface of the moon, and I’d have to start all over again.
‘3M’s Atherstone facility is tailor-made for the job. It’s big enough, it’s climate-controlled and it’s got a great spraybooth, with all the preparation areas and stations right in front of it. Everything you need to prep and paint this vehicle is right on hand and ready to go. It works so seamlessly.’
3M’s adhesives have also been used to bond parts made of carbon fibre and other composite materials, ensuring the car is as lightweight and durable as possible.
3M technical supervisor Gavin Phipps said, ‘We couldn’t miss the chance to be a part of the production of this amazing vehicle. We hope 3M’s contribution, from both our products and our facilities, will help the Bloodhound to make history.’