Master Abrasives supports BLOODHOUND SSC
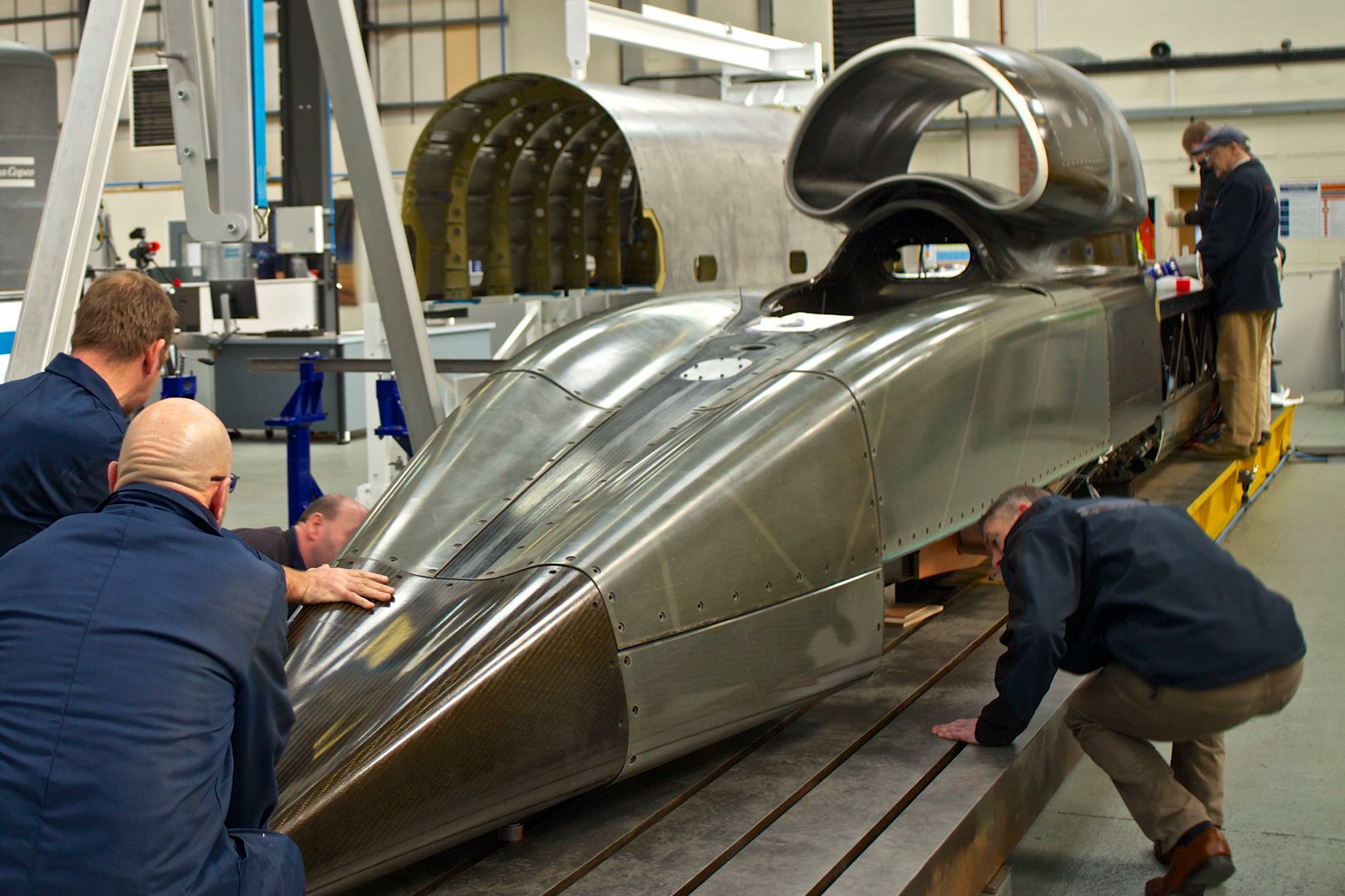
Master Abrasives seized the opportunity to become a product sponsor for the BLOODHOUND Project when they were approached by the team in 2014. As part of its support for building the fastest car in the world, Master Abrasives has supplied a selection of high performance abrasive products for use both in the workshop and in the actual build of the 1,000 mph BLOODHOUND Supersonic Car (BLOODHOUND SSC).
The BLOODHOUND Project is a unique engineering adventure designed to inspire the next generation about Science, Technology, Engineering and Mathematics (STEM) subjects with the hope they will be motivated to enjoy engineering and potentially become the engineers and scientists of the future, which this country needs to allow us to remain at the forefront of technological developments.
Master Abrasives was initially asked by BLOODHOUND to supply some abrasive quick change discs for use on hand held air tools. Chris Dee, assembly and build lead at BLOODHOUND said, ‘Here at BLOODHOUND we use a lot grinding discs, barrel sanders, belt sander, bench grinders etc. we felt that Master Abrasives range provided the coverage we need for the full spectrum of materials used on BLOODHOUND SSC from Titanium and carbon fibre to steel and plastic. Master Abrasives not only offered us the vast range of product but as importantly their expertise.’
One of the applications that the quick change discs supplied have been used on is to grind the Titanium outer skin on the upper chassis of the car around the rivet holes. The BLOODHOUND technicians were impressed with results when using Master Abrasives products, Chris explained, ‘Our task became more difficult when we faced the prospect off abrading the Titanium skins that make up the upper chassis, these all required roughing up to allow the bonding process between rib and skin to be effective. The Master Abrasives engineers provided us a great solution after consultation about the task: using ceramic coated discs which did a really great job in achieving our objectives. When you combine using the ceramic discs with our Atlas Copco tools the results are very good indeed.’
The products that the engineers on the BLOODHOUND Project team originally used were the TR (or ‘Roloc’) fitting with an aluminium oxide abrasive grit. The Master Abrasives solution was to supply them with a TS (or SocAtt) fitting as this increases productivity being faster and easier to change than the TR type, as well as a more solid and secure fitting system.
Master Abrasives products have also been used to finish the carbon fibre moulding for the cockpit and air intake to prepare the surface ready for painting. In addition, a selection of conventional abrasives for general use has also been supplied to the BLOODHOUND workshop. ‘There are many applications where the Master Abrasives-Atlas Copco combination works well from the Titanium floor to the orbital sanding discs to rub down carbon body work. Additionally Master Abrasives are all round good guys. Thanks for your help.’ concluded Chris.