The crumple zone
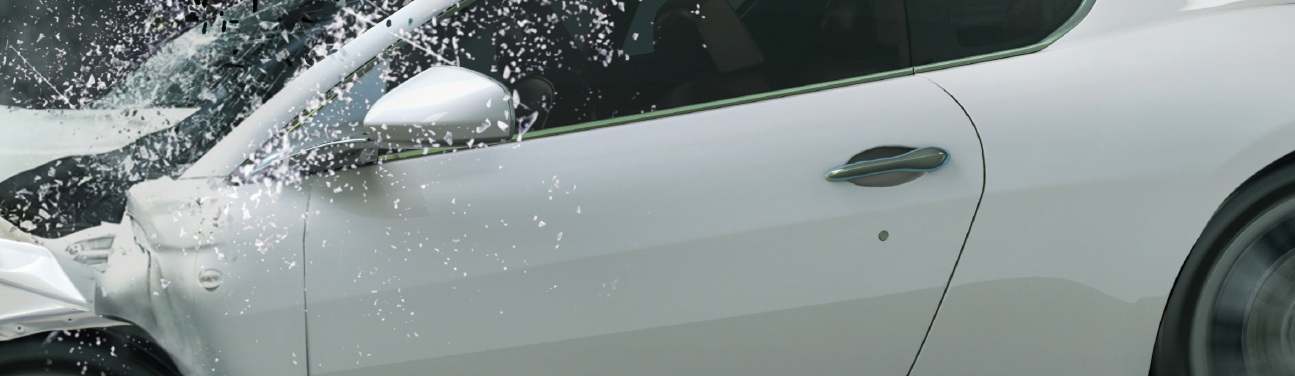
In last month’s issue we reported how crumple zones and airbags are amongst the safety features that have contributed to a 50% decrease in UK road deaths. Crumple zone, deformation zone or crush zone; call it what you like, we’re all aware of the modern car having these zones at the front and rear
Crumple zones have more than one purpose. Firstly, they are to extend the time period of an accident, to gradually stop the human occupants and reduce the likelihood and severity of life threatening injuries by graduating the deformation of the vehicle into the rigid safety cell area. Secondly, they can limit smaller, lighter impacts into an area that is designed for repairability, typically consisting of bolt-on panels and components, or defined cut and replace zones.
Engineering a car to be able to accurately and consistently predict how it will behave in a crash is an advanced science. I say ‘consistently’ as it needs to perform reliably and protect occupants in whichever market the car is sold. Manufacturing engineers often seemingly ‘grumble’ about the challenge of developing a car to perform in different crash tests around the world, but, in reality, these differing demands have probably challenged and pushed them to develop the hugely positive increases in safety we see today.
Pedestrian
Pedestrian safety has been an area of considerable attention. From the early days of focusing on car-to-car accidents, the world moved on to realise there are many other vulnerable road users; pedestrians, children and cyclists all needing protection in a collision with a car. The design of bumpers, bonnets, front wings, and even headlamps and bulkheads have evolved to direct and absorb the ‘human’ aspect of an accident. I mention bulkheads here as, in some cases now, this panel may only be connected on three edges, effectively giving it freedom to flex to create a softer zone at the base of the windscreen. Bonnets are now designed to allow a thin, flexible skin to deform into a stronger frame which it does in a controlled fashion, into an increased space above the engine. And, we are all aware of wing mounting brackets that are designed to flex with the wing panel at the crucial intersection – where the bonnet and wing meet.
Deformation panels or crash cans themselves are the focus of much engineering. Some of these are in complex shapes to absorb impact forces by collapsing at a programmed rate. The new Volvo XC90, for example, has six chambers in each crash can that are bolted at both ends to support repairability and to absorb impacts. Another manufacturer is researching how to bond these crash cans on with new adhesives that enable sufficient flex to allow these panels to deform rather than ‘snap off’. If this solution comes to market, the repairer will need to remain very aware to ensure the correct adhesive is applied in replacing these.
Impact
The impact-absorbing structures themselves are evolving. As we know, the percentage of advanced materials in a modern car has increased significantly, to reduce weight and strengthen the structure for side impacts (an area that has little room to deform because of the proximity of the occupants) but this, in itself, causes problems. Again, citing the Volvo XC90 as an example, you could not increase the boron steel content much further as boron steel does not deform, meaning that for the front and rear structure, its applications are limited. So, new trends are emerging, enhancing the already multiple impact load paths to cope with more severe impact cases.
We know that frontal impact forces are already distributed by the front structure, including the chassis legs and wheelhouse panels, into the under floor area, and through the A post and sill. But, by creating very specific nodes, the engineers are now dissipating these energies further through ultra-high strength steel (UHSS) transmission tunnels, through the doors and, in cases of offset impacts, channelling forces through to the opposite side of the car. The vehicle damage assessor (VDA) needs to be very aware to check all potential load paths for deformation. This is even more critical for structures that include areas that do not deform, or for modular mixed-material bodies such as those with carbon fibre tubs. Here, the energy can be transmitted to the opposite end of the vehicle or into relatively brittle components such as aluminium castings.
Equally, we need to remain aware that the front sub-frame is also typically being used as a supporting load path, so the alignment and mounting of this needs to be considered too.
Complexity
With this level of complexity, which continues to increase, the challenges in engineering, production and repair will not abate. The inclusion of a greater variety of materials adds to this, as different materials have different properties of rigidity and strength. This requires a lot of thought for joining, in production, and will require just as much in repair. As I previously mentioned with the adhesive bonded crash cans, being strong isn’t enough. If it’s too rigid to allow a controlled deformation; the panel would just collapse.
And, with the rise of electrified vehicles, whilst a chassis leg may need to deform to absorb front or rear impacts, it may need a higher degree of lateral stiffness to protect a high voltage battery pack for a hybrid or battery electric vehicle. The XC90 provides another excellent example of advanced body engineering as the plug-in hybrid powertrain model features stiffer rear floor and inner sill panels, and a transmission tunnel (where the battery pack is located) that will not deform.
Test
The small overlap crash test requirement is another challenge. Vehicles do not often collide head-on, in many cases just a glancing impact which, as you can imagine, is outboard of the chassis legs for both vehicles, resulting in an A-post to A-post impact of two very strong structures. Meeting this impact type has resulted in two engineering strategies. The first is for filler panels from the bumper beam-ends to channel the impact forces into the chassis leg on the appropriate side, sometimes even channelling some of the impact force along the beam and sub-frame to the opposite side. The other solution is to engineer the structure to direct the force of the entire impact to ‘bounce’ the cars off each other so that the non-deforming A-posts do not engage each other heavily; though this also places requirements on the supplementary restraint systems (SRS) to protect the occupants from injury resulting from the lateral movement of the vehicle.
A technical minefield? Yes, but we have known vehicles are rapidly growing more sophisticated for a fair few years now. That’s why it’s not enough to just assume a certain material and joining method, and why it’s not as simple to assume what we can see is the full extent of the damage.
Creating and developing a modern car to meet the myriad of potential accident scenarios is extremely challenging and takes up a big chunk of the billions of pounds of research and development spent by vehicle manufacturers each year. It is why UK insurance companies invest in Thatcham to help support our repair industry in safely and effectively repairing these sophisticated structures. We work hard to make data, advice, methodology and training available for you to manage a task that frankly, isn’t going to get any easier.