Right move
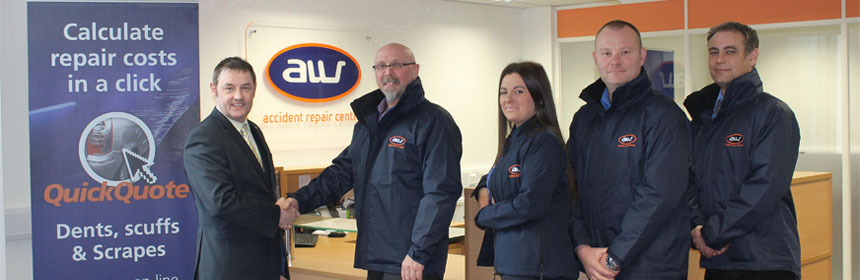
AW Repair Group opened its fourth site, based in Markham Vale, Derbyshire, in March this year. It’s yet another step on what is proving to be a steady, highly considered expansion of the group’s territory – a strategy which is likely to continue. bodyshop magazine’s, Mark Hadaway bore the steady flow of the M1 roadworks to find out more.
AW Accident Repair Centres (Derbyshire) could not be more conveniently located just off junction 29a of the M1 at Markham Vale Enterprise Park. The new hi-tech 15,000sqft facility secured the PAS125 Kitemark accreditation a little after three weeks from officially opening and already has a number of plans in place to further its potential. ‘We are in the perfect location,’ explained Jade Johnson, business development, marketing and communication, AW Repair Group. ‘With direct access to the M1 and Chesterfield town centre on our doorstep, it provides us with a great opportunity to continue to build our portfolio of work sources.’
The majority of work is currently coming via its insurance approval partners however the business is exploring the potential for other opportunities – namely vehicle manufacturer approval and retail.
‘We are currently exploring the options in the area to gain a vehicle manufacturer approval,’ explained Jade who points to the fact that sites across the group currently holds Land Rover and Volkswagen Group approvals, including structural aluminium for Land Rover and Audi, as well as boasting a reputation as a Porsche specialist.
Develop
The retail side of the business is an area Jade is keen to replicate and the new AW site is very much geared up for growth in this area with a swanky, open plan reception area offering free wi-fi for customers, along with three dedicated fast track repair bays for ‘while you wait’ and one day repairs mirroring its prestige site in Lincolnshire. Two multi-skilled technicians are currently dedicated to the fast track operation.
Reinforcing the retail philosophy across the AW Group is the development of its app which offers an online quoting facility, vehicle progress tracking via the bodyshop management system and customer service index (CSI) reporting. An overhaul of the existing website is also imminent to enhance its user friendliness. An excess protect scheme is also offered as a means of ensuring customer retention.
Related to the retail proposition, at an operational level, AW Group has also introduced a mobile repair unit which offers a service based on up to two damaged panels in size. Operating out of the Nottinghamshire, Newark site, the unit has proved a popular addition to the AW Group offering and the potential is there for more to follow.
Leading
Back within the four walls of AW Accident Repair Centres (Derbyshire), as you would expect, the business is fitted-out with some leading edge equipment including, Audamobile; eight metre drive-through Junair Spraybooths complete with energy packs, LED lighting, iSystem touch control and quads drying system; a 12 module Minden dust extraction facility complete with energy saving auto remote switch-off and integral three phase for multi-bay operations; a three bay Blackhawk Korek in-floor pulling system, complete with ramps; a Car-O-Liner Bench Rack 5000; PPG’s refinish system; Stanners panel repair system, and energy saving devices such as LED lighting and radiant heating. It all makes for a very clean, efficient and environmentally sound work environment.
Processes within the Derbyshire site have been successfully integrated from the group’s three other sites, with the Sleaford site being the main influencer of the workshop footprint and practices. Several employees have also been transferred over from existing sites as a means of providing consistency to the operation.
Managing director, Andrew Walsh explained, ‘Some of our work provider partners committed to the new site immediately on inception and I’d like to take this opportunity to thank them for being part of AW Repair Group’s continued development. It is early days but business is good and we are within reach of our initial capacity.
General manager, Ian Pearson added, ‘We have a fantastic team and the skillset at our disposal is extremely high, and has been commented on by the likes of our paint partner, PPG. It is very exciting to be involved in building the business’.
Consistency
A key area of focus for AW Group is on ensuring consistency across the business and, as such, Gemma Goodban assumes the role of group compliance manager. Her role is to standardise the practices across all four sites through ensuring adherence to AW’s tried and tested procedures.
‘Having worked for AW as a customer liaison advisor and then manager for 10 years, I’ve seen how we as a business need to regularly respond to changing customer needs but ensure best practice is standardised across the group,’ said Gemma who oversees work provider service level agreements across all sites.
‘It is intrinsic we have processes the same across all sites,’ explained Andrew. ‘The Nottinghamshire, Newark site is our central hub for deployment, enabling us to manage capacity across the group, however our Lincolnshire, Sleaford site is our prestige repair centre, head office with accounts and central customer service call handling, providing our work partners with the ‘one point of contact’ they require.’
Additionally, Andrew points out every single document to pass through AW is held on file within its digital archiving mainframe, ensuring precise and evidenced paper trails for all stakeholders.
Evidence based information is at the centre of AW’s business and, over the years, it has developed its own inhouse systems and protocols, something it deploys succinctly across all sites. ‘During the severe winter of 2010/11, when work volumes rocketed, we developed a volume calculator for the business,’ explained Andrew, who admits to being ‘data hungry’.
‘The concept has today evolved and developed into our unique daily operating control (DOC) which provide us with clear, precise, real time information across all four sites.’ Each week the business generates performance and financial key performance indicator reports ensuring targets are being met with a speedy reaction to positive and negative trends.
A management meeting takes place once a month across all sites and, similarly, a monthly vehicle damage assessor’s meeting also takes place – it’s all part of AW’s strategy to maintain brand image and standards across the board.
‘Our utilisation of data provides us with a very powerful tool,’ said Ian. ‘There are many demands on the business and we constantly need to ensure we are the right side of simply being busy. We understand exactly where the ‘sweet spots’ are across our sites and achieving them consistently is the aim.’
Recognised
It is this consistent approach to business which puts AW Group in the position it is today – a recognised brand, providing a quality service.
‘Undoubtedly, there are pressures within this industry,’ said Andrew who believes much of the group’s success has been down to recruiting the right people – something which, as the brand develops, becomes increasingly self-perpetuating.
‘As a business, we attract people with similar values to our own – honesty, integrity and loyalty. And that is a fundamental reason that we have such a good team throughout the business – something I am very proud of,’ said Andrew.
With what seems like solid foundations upon which to build are we likely to see further expansion of the AW foothold? Well, it’s not a definitive answer either way. ‘A fifth site is probable but it will need to be the right time and the right place,’ explained Andrew.
‘We have typically employed a greenfield site model of expansion but that’s not to say if the right acquisition target became available we would ignore it. ‘Our priority though, at present, is to get this site (Derbyshire) up to full potential and continue to provide the levels of service people expect of our brand. As we have proved in the past, any future developments would need to align with that AW Group philosophy.’