Home and dry – Drying feature
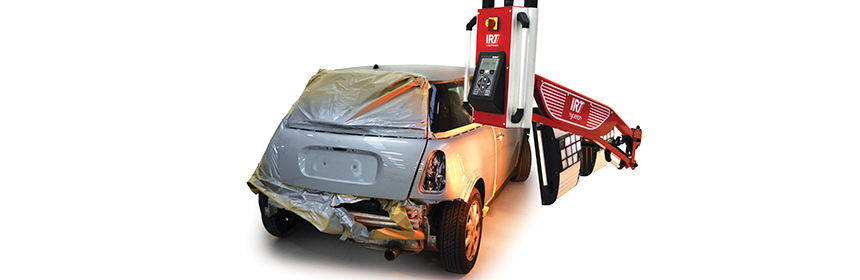
Whether it be paint, processes or products, curing and drying is crucial to the speed of turnaround.
bodyshop’s Padraig Mallett talks drying systems with the experts to find out more.
The bottleneck within a traditional bodyshop has typically been the spraybooth. With the rapid turnaround of vehicles constantly under scrutiny, the ‘paint’ element, and in particular drying, has come under increasing pressure in bodyshops. A major focus is centred on ensuring a vehicle only needs to go in a booth for the final finish (and the least amount of time). Paint manufacturers have a major role to play here and, as a direct result of industry feedback, they have created infra-red drying systems, ultraviolet (UV) products and air drying materials, all designed to help reduce energy costs and improve drying times.
Whilst new technology, such as infra-red and UV, has played its part, the technology used to formulate the paint is a key element in the success of these processes. A number of the latest paint systems include express drying activators to reduce the curing times at low temperatures. However, to ensure a high quality finish, accurate heat control in the paint drying is absolutely essential during the flash-off and bake, including a very controlled ramp-up in drying temperature.
In response to market demand for fast drying products, AkzoNobel introduced its Sikkens Autoclear Rapid Air AS. With fast, dust free times at all temperatures, it aids in accelerating the express repair process and enables bodyshops to increase their volume of work.
Fast
Short-wave infrared is increasingly being used to provide fast drying at low energy electric cost. Car manufacturers around the world are using infra-red at the end of their high volume production lines in order to provide fast refinishing of any paint defects. IRT branded infra-red, is supplied in the UK exclusively by Bodyshop Solutions is used extensively within major UK car manufacturers for their refinishing processes. According to Bodyshop Solutions it provides the required fast drying times at very low energy cost, and is coupled with excellent temperature control for high quality results. It also offers ease of use for the operator.
Bodyshop Solutions is now the preferred supplier for the Fix Auto repair network in the UK, a business which is pushing the ‘fast repair’ ethos through its new Fix & Go sites. This fast repair goal is a growing trend in bodyshops across the UK, as it enables more efficient and higher throughput of repairs, means customers get their cars back quicker and reduces claims costs for insurance companies. In combination with faster drying paint products and new bodyshop work processes, short-wave infrared is a vital element in this fast repair culture for the rapid curing of both fillers and paints.
Infancy
UV paints are still in their infancy in the UK. UV radiation allows UV paints and lacquers to cure very quickly. In contrast to conventional coatings, UV formulations contain little or no solvents. In a UV curing process, polymerisation photo-initiators are activated by intensive UV light. Chemical compounds are then broken down and cross link to form new compounds, meaning that in fractions of a second the cross-linked system is dry and abrasion proof and suitable for further processing. A number of bodyshops in the UK are using UV cured primers and clearcoats, but there is still a long way to go before they are more widely adopted, as although they provide the benefits of very fast curing they can be more expensive than standard paint products. To cure UV paint products, IRT has developed a range of UV drying equipment, either as standalone UV or as combination UV/infrared equipment.
Different
Some suppliers are now looking further afield for different solutions because of changing climates and conditions that can occur in bodyshops. The temperature of the bodyshop, hot or cold, can affect the way the employees operate, their methods, and their output, especially if cars are constantly coming in and going out of the bodyshops’ doors, as this can change the environment quickly.
High humidity or rain will make the painters’ job more difficult as the conditions can affect the panels and/or vehicles, an endothermic panel system can be installed in spraybooths, allowing parts to be pre-heated to dry faster.
However, the old rules still remain true for bodyshops. Making the most of any spraybooth and drying system is fundamental, as is using as little energy as possible. The cost for energy has risen substantially, despite the recession, adding to the repair pressures already on repairers’ shoulders.
Efficient
Bodyshops have to constantly think of the most efficient and practical way of drying panels and judge which jobs can be tied together. Planning ahead and assessing any upcoming jobs one way to ensure this is happening.
Organising the bodyshop around the drying of vehicles and parts is fundamental, which is where the bodyshops’ structure, processes and employees are called into action. Drying systems are not the same and unless preparation is carried out, quality can suffer.
The quest to achieve a faster drying solution is never ending and drying equipment manufacturers are already looking to the future, with new solutions being trialled. An aspect they are continually trying to improve upon is the movement of air around the drying area, which aids the speed of drying.
The quick air drying (QAD) system, developed and patented by Junair, is an advanced auxiliary air movement system that supplies airflow from the corners of the cabin and was designed for use with coatings that comply with current legislation. This system is also available for retro fit installation into any make of spraybooth oven. Bodyshops using QADs can expect an overall paint process which is 35% faster and can save up to 40% off its energy costs. Some industry insiders believe that the technology for the future of drying will be endothermic systems that are installed in spraybooths.
While many advancements have been made in paint and drying solutions over the past few years, manufacturers are continuing to invest and explore new ways to speed up the drying process, the next big thing in drying technology could be just around the corner. One thing you can be sure of, is that the focus on drying and achieving a quick turnaround in bodyshops will continue to be a major discussion point within the repair industry.