Developing talent for tomorrow – Training
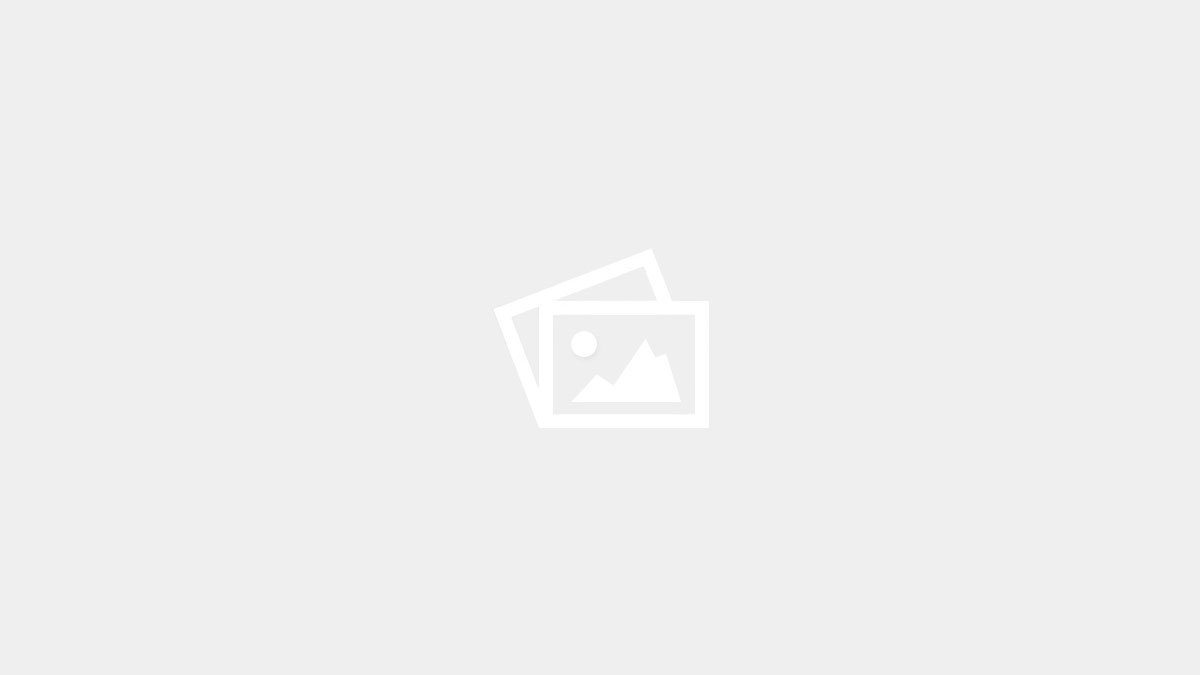
There is currently a big focus within the bodyshop sector on the training of apprentices and upskilling existing personnel. Here, bodyshop’s Padraig Mallett takes a closer look at the training that currently exists and what is being done to overcome an emerging skills gap within the sector.
Two-time winner of bodyshop’s education award, Riverpark Training and Development is a training provider for students in body repair, vehicle fitting and vehicle refinishing. It also works with Thatcham to provide IAEA training and assessment on site and also training for VDA. Riverpark’s training team has a specific interest in supporting and developing young people to meet the needs of employers.
Since 2007, the repair industry, like many others, has been under pressure with many staff transferring to other jobs requiring their skill sets. Many of these skill levels are hard to replace; years of experience on mechanical electrical and trim, panel and paint is not readily available and has to be earned. Colin Hagan, Riverpark’s managing director, said, ‘I know of no other industry that is so highly regulated, requires high skill levels and yet gets paid so little in profit margins to make it function.’
Attract
This makes it very difficult for the industry to attract the right calibre of young person into the sector. It’s clear the UK has the ability to produce highly skilled people but according to Colin, they aren’t given enough recognition. ‘In Germany, for example an engineer holds the same status as a doctor.’
‘What do we do? We educate our young people to be doctors where there are no jobs. I do believe however the tide is turning on this and central government now recognises the need for change but a long-term strategy is required instead of the usual two year quick fix.’
In Colin’s opinion, apprenticeships need to be given more recognition, further regulation needs to be introduced and pay increased, in order to produce the technicians that can repair the ever increasing complexity of the modern vehicle correctly.
There have been a lot of developments in vehicle construction and design over the last 10 years and the industry has embraced these changes. And although some may not have welcomed the introduction of PAS 125 or its newly superseded BSI 10125, this protocol has ensured everyone is aware of the complexity of modern practices, which are vital to make sure vehicles are repaired correctly. As suggested in the words of a former employer, ‘if you stand still in this industry you will end up going backwards’.
With technology and repair procedures such as the rivet and bond processes now widespread, developments are continually taking place within the equipment training sector, which surely puts extra burdens on struggling bodyshops. ‘Keeping a profit margin that will allow companies the ability to invest in new equipment, new staff and training are the main challenges facing our industry currently,’ said Colin.
Demand
‘I see the demand for bespoke training increasing over the next five years, as a training provider we have identified significant areas where we need to increase our own knowledge and we have currently put an up-skilling plan in place. After all, we need to meet the needs of the accident repair industry as best possible and provide sensible advice as to where their technicians need training.’
The biggest challenges for new recruits in the accident repair industry is now the complexity of repair. New technologies are emerging yet, as a sector, many are just getting to grips with the existing, complicated insurance schemes, the ever demanding drive to achieve hours sold, different repair methods and varying composite components.
Work ethic is critical to any person entering employment but according to industry insiders, in recent years this has been in decline. As with any career path, you only get out of it what you put in. Colin said, ‘As a training provider placing students with employers, time and time again we recognise it is about having the right attitude.’ Riverpark has been very lucky to see five students progress to World Skills recognition, ‘with the right commitment and work ethic this is achievable by anybody entering our industry,’ said Colin.
Advancements
Another training provider currently making advancements in the bodyshop industry is Babcock International Group (Babcock). Kieron Bramall, Head of Automotive at Babcock agrees with Colin in regards to the ongoing need to attract and retain qualified and capable staff within the bodyshop network. To assist, Babcock is working to meet this challenge and prevent any further growth in the skills gap within the sector.
‘There is a perception among the wider public that the industry is dominated by the types of ‘garage under the arches’ that are seen on some television programmes. This couldn’t be further from the truth. The industry can offer a technologically demanding and stimulating career in a modern work environment. We are working closely with industry bodies and our customers to change that perception and attract premium candidates to join and stay within the bodyshop network,’ said Kieron.
The growing skills gap within the industry can be contributed to the rate of change in vehicle technology. This is not just about vehicle electronics and the latest electric and hybrid vehicles but also in body materials such as carbon fibre, exotic materials and the subsequent construction and repair techniques needed to repair the cars to the manufacturer’s specification. This is likely to overtake the current knowledge and skills of the existing work force unless there is the training provision made available, in a format that meets the industry’s current and future needs and maintain the technician’s competence.
Initiative
AutoRaise is one initiative, created by repairers, to address the acute skills shortage of the repair industry. It has approached the government and they have approved its proposal of a new apprenticeship standard aimed at benefitting repairers, to help them meet the needs of the modern day pressures in our industry.
‘Training is constantly evolving to meet the requirements of the fast paced, technologically complex automotive industry. From experience, and from speaking to customers, we are seeing a move towards more eLearning for the theory based elements of the training experience. This can vary in its complexity from virtual classrooms and 3D environments, to online reference libraries and ‘how to’ video guides,’ said Kieron.
E-learning is a flexible concept which reduces the need for travel and time away from the business, thereby saving costs and increasing productivity. In a response to customer demand for more flexible training, Thatcham Automotive Academy has adopted this approach to skills development in the UK collision repair sector. For the learner, access to the materials can be gained 24/7 meaning that they can learn at their own pace and in their own time. The trainers can monitor the use of eLearning and tailor their training accordingly.
Modern training facilities also have a role to play, and the increasing use of virtual reality spraybooths in which techniques can be refined will also be an evolution.
It is clear that training workers within this industry comes with its own set of challenges. However, it is also clear from speaking to training providers there is a lot being done in terms of training and upskilling, to ensure the industry stays in step with the ever changing automotive landscape.